7 top 2020 manufacturing trends
09 Jan, 202010 minsThe age of automation is here. As we start a new year and a new decade, we’ll begin to see m...
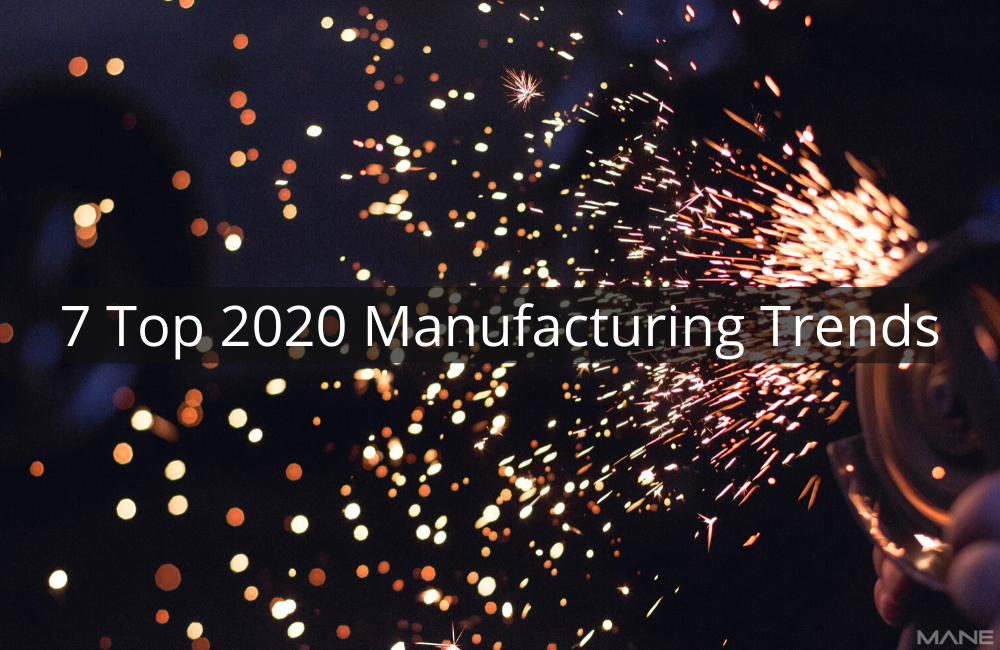
The age of automation is here. As we start a new year and a new decade, we’ll begin to see more and more signs of a future where advanced technology will lower operating costs, improve efficiency, streamline production through new planning techniques, and help companies and organisations better support their customers.
So what will that future really look like? Here are 7 trends experts predict will go mainstream in or just after 2020:
1. Closer Alliances between Humans and Machinery
We’ll begin to see assistive technologies such as HMI, robots and PLCs become the closest allies of human workers. Using virtual and augmented reality interfaces, cooperation between mind and machine will be almost seamless, allowing for easy visualisation of new products. Automotive design engineers will be able to walk around inside their schematics to develop a better understanding of each part and process. Designs can be modified even before the development of a prototype, saving companies money and reducing the likelihood of errors.
2. Continuous, Real-Time Analytics
Cars, homes, and other environments are being designed with more and more potential for connection to the IoT--and manufacturing environments are poised to join that list in droves. Industrial processes are already being designed with cloud-connected sensors, allowing data to be collected and analysed on an unprecedented scale.
3. Usable Big Data Resources
These sensors will collect billions of individual data points--so many that in the past it would have been impossible to process and analyse them in real-time. Now, though, big data processing technology means manufacturers can use them to make decisions on the fly about how to improve performance and optimise production, as well as to detect potential issues before they happen.
4. Greater Reliance on Predictive Maintenance
One software service management company predicted that most companies lose £60,000-£500,000 a year because of unplanned outages in their machinery. In highly automated manufacturing plants, a machine or system may fail as often as every two and a half months. Predictive maintenance technology--which monitors every machine and recommends fixes in advance--is estimated to cut these sobering numbers in half.
5. Live Resource Planning Support
Another source of real-time data will be resource planning software. This is basically predictive maintenance for business operations--it helps companies make empirical decisions about what to tweak and where so that productivity loss from unexpected downtime can be reduced even further.
6. 3D Industrial Printing
We’ll see a reduction in the cost of many machine components that can now be printed in 3D. Manufacturers will even be able to produce the parts they need on-demand, reducing supply and storage needs. Processes that once took months will be cut down to days.
7. Better Supply Chain Management
Businesses everywhere will see their supply chains become more transparent, making their inventory easier to control, their profits more competitive, and their customers more readily satisfied.